I am committed to acoustic guitar innovation. Nearly every part of my acoustic guitars is bespoke or has been designed or built using an innovative process. Listed below are ten innovations that I have been responsible for or played a significant part in; there are many more that I have not listed. These innovations offer direct benefits to the player in terms of sensitivity, playability, musicality, longevity or cost reduction. Few acoustic guitars offer even one benefit to the player resulting from innovations of this type, whilst the majority of my guitars will contain all ten.
Nut and Saddle Compensation
Nut and saddle compensation make my acoustic guitars play much more in-tune to the equally tempered scale than most other guitars. This makes them sound more musical with more clarity as a consequence of congruent harmonics across strings. Sure, nut compensation goes back a while, but the techniques used are often fairly primitive or fall into the “one size fits all” category. The amount of compensation required is different for every set-up and every player. It depends on the string type, active string length, the height of each string above each fret and how much pressure the player uses to fret a note. Change any of these and you need a different solution. My computerised techniques allow nut and saddle compensation to be computed quickly (for standard string sets) for both classical and steel string guitars and for standard and non-standard tunings. I have invested a considerable amount of time measuring string properties, so I can get most results quickly. If I need to measure string properties (usually only for non-standard strings) it takes me a little longer.
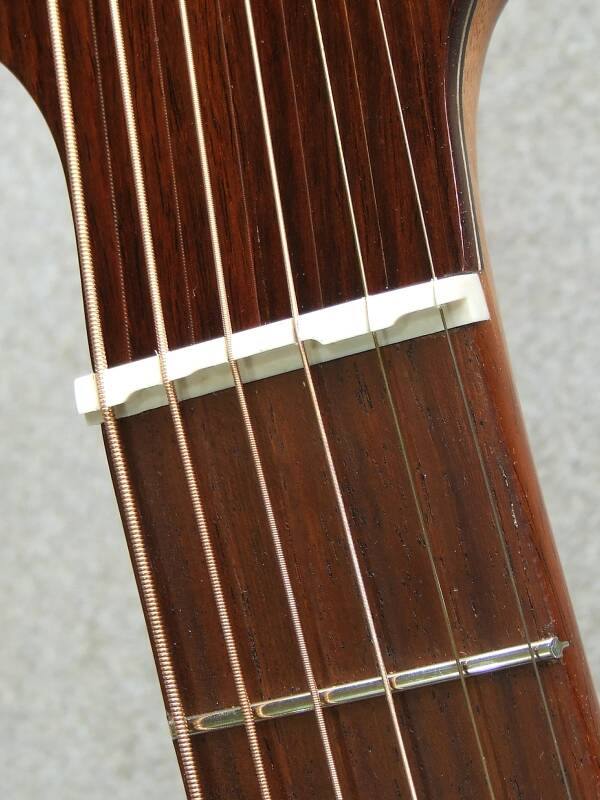
Falcate Bracing
I designed my Falcate bracing system to escape the limitations of more conventional bracing practices. The system is configured to withstand the high twisting forces exerted by the strings over the saddle onto the acoustic guitar’s top (tending to rotate the saddle downwards and towards the sound hole) whilst still allowing the top great scope for vibration. There are two major benefits: the stiffness distribution makes for a more even sound across all notes (i.e. there is no “designed in” bias towards a particular frequency response) and there is increased monopole mobility (responsiveness and volume) without compromising longevity, because the strength and stiffness (and consequentially the mass) is where is it needed and not elsewhere, making for an efficient design.
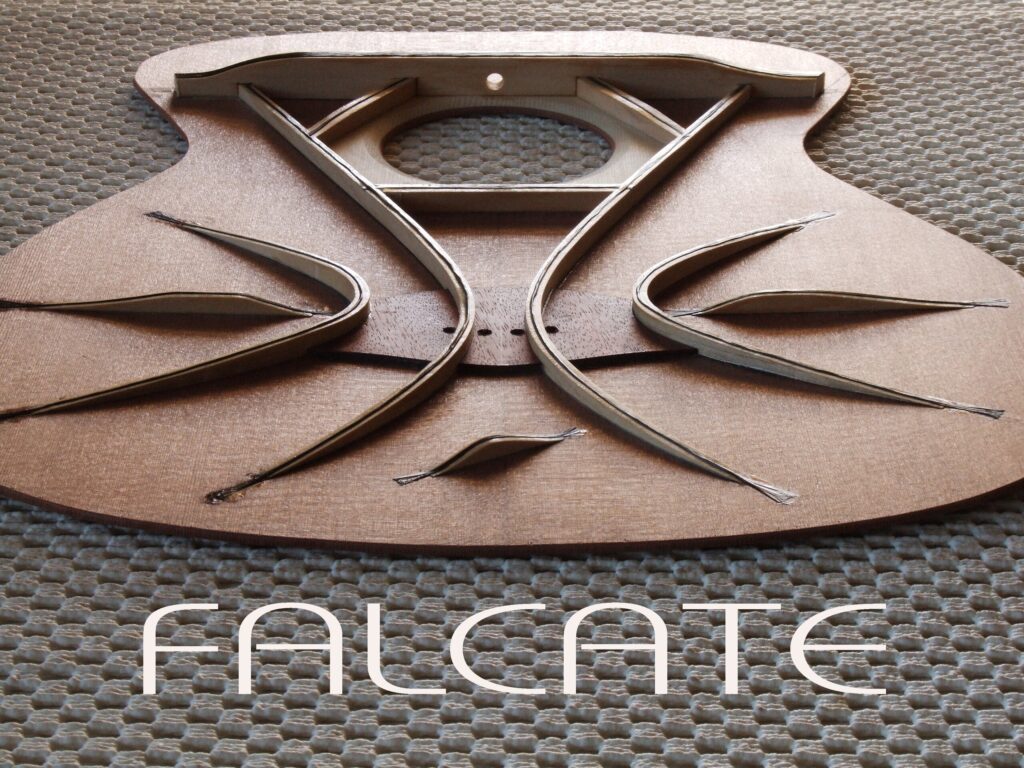
Top Thickness
Every top and back panel I make has its material properties measured and is thicknessed accordingly. Some custom makers measure or sense the material properties and then guess how thick to leave the panels, but I have not come across anyone else who can determine how thick an acoustic guitar panel should be with engineering precision. The method I use takes a whole lot of guesswork out of making acoustic guitars which means that I can consistently achieve the target vibrational performance and always produce a responsive guitar. It means that I can consistently achieve the right relationship between the vibrational performance of the back and the top and so shape the sound to how I want it.
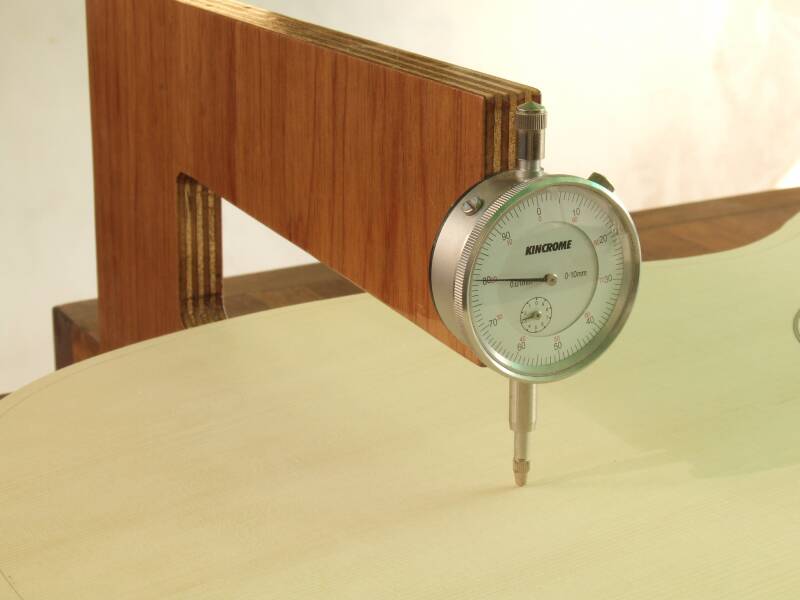
Carbon Fibre Reinforced Bridges
An acoustic guitar’s bridge is more than just the place where the strings terminate. It is an integral part of the bracing structure of the guitar top, though most people don’t think of it in that way. It is a significant mass (most bridges are made of ebony or rosewood) and on some designs a significant stiffness. The sound produced by a guitar is dependent upon the acceleration of the bridge. More acceleration=more sound. Low mass bridges accelerate more under the oscillatory string forces. My bridges are ultra low mass, generally made of non-conventional woods (i.e. seldom of ebony or rosewood because they are dense woods) and are reinforced with carbon fibre for strength and stiffness. My bridges are typically less than half the mass of other makers’ for both classical and steel string guitars. The benefit is much more volume.
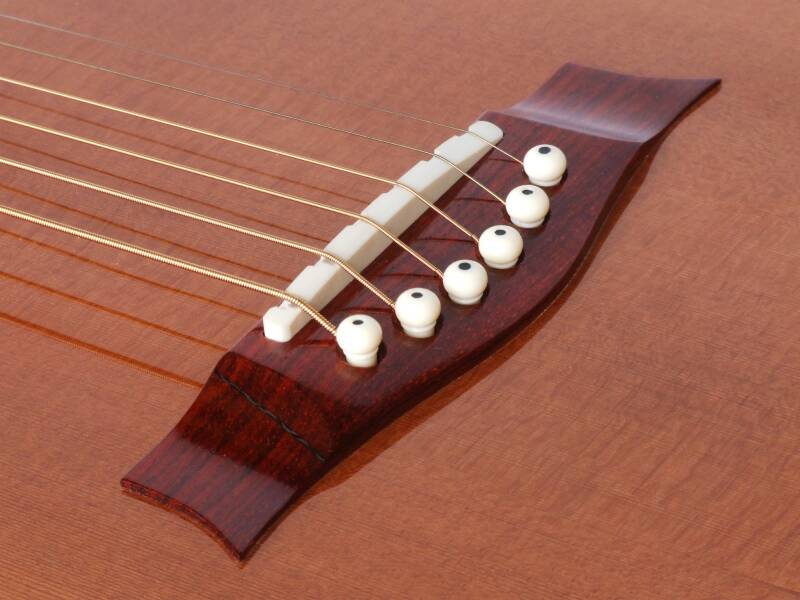
Heavy Sides
This innovation is a major breakthrough in acoustic guitar design. I discovered the effect when I was testing guitars in their building mould, which adds considerable mass to the sides of the guitar. The frequency response of the guitar was different when it was in the mould to when it was out of it. The effect can best be described using a firearms analogy. When you fire a gun the bullet accelerates out of the barrel and the shooter experiences a recoil from the gun – the gun accelerating towards the shooter. If you immobilise the gun e.g. by holding, say, the butt of a rifle against a tree, or by making the gun heavier, the gun accelerates backwards less and the bullet accelerates forwards more. Same with a guitar; make the sides heavier and the body of the guitar accelerates less and the top accelerates more. The more the guitar top accelerates under the string’s oscillatory forces the more sound it produces. Having observed the phenomenon experimentally, I proceeded to model it mathematically to understand whether the effect was real or just some strange aberration. It’s real. The concept can be used to great effect in shaping the volume and tone of an acoustic guitar. How much mass to add, where to apply it and how to apply it are critical to the effect produced. It is a benefit I have available as standard on all my guitars, classical and steel string and it is truly unique.
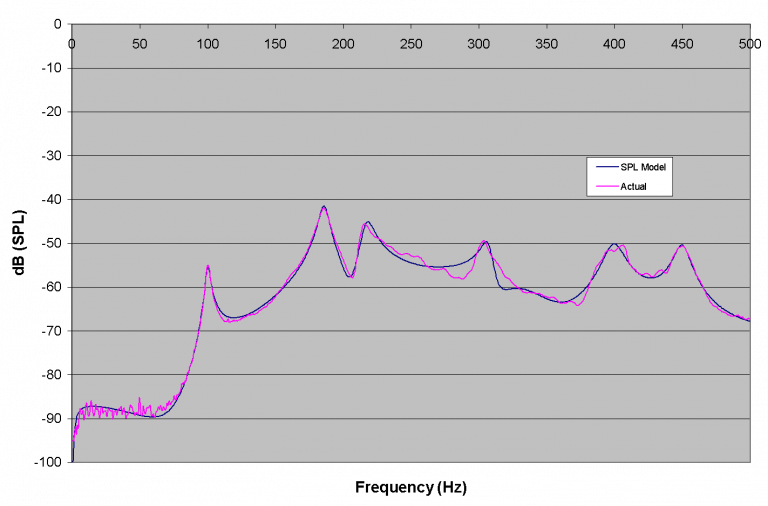
Acoustic Guitar Neck Joints
All my fixed neck guitars, classical and steel string, feature a neck that can be detached by unscrewing just four bolts from inside the guitar, picture left, below. Bolted necks are nothing new for electric guitars; Leo was doing it in the 1950s. However, having a detachable, bolted neck on an acoustic guitar which is easy to adjust for angle (if it ever needs it), with solid wood beneath the fretboard from the nut to the 18th fret, with a truss rod that is adjustable via the sound hole (so the headstock isn’t weakened) is certainly rare, if not unique. One reason for this innovation is that I hate dressing frets, especially the very hard frets that I use. Building necks this way means I can fret with such precision that I very rarely need to fret dress and the plane of the top of the frets remains very stable over time. This benefits both the playability and longevity of the guitar.
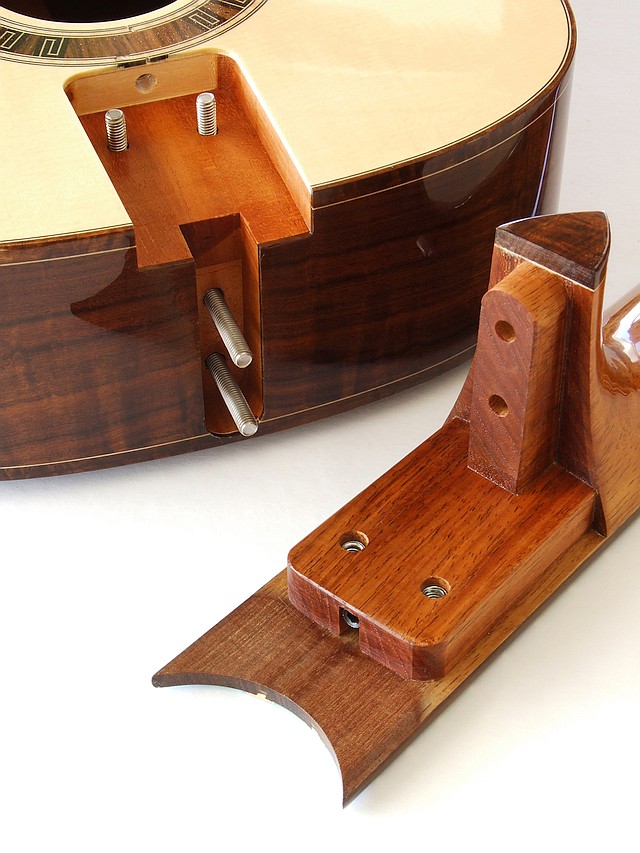
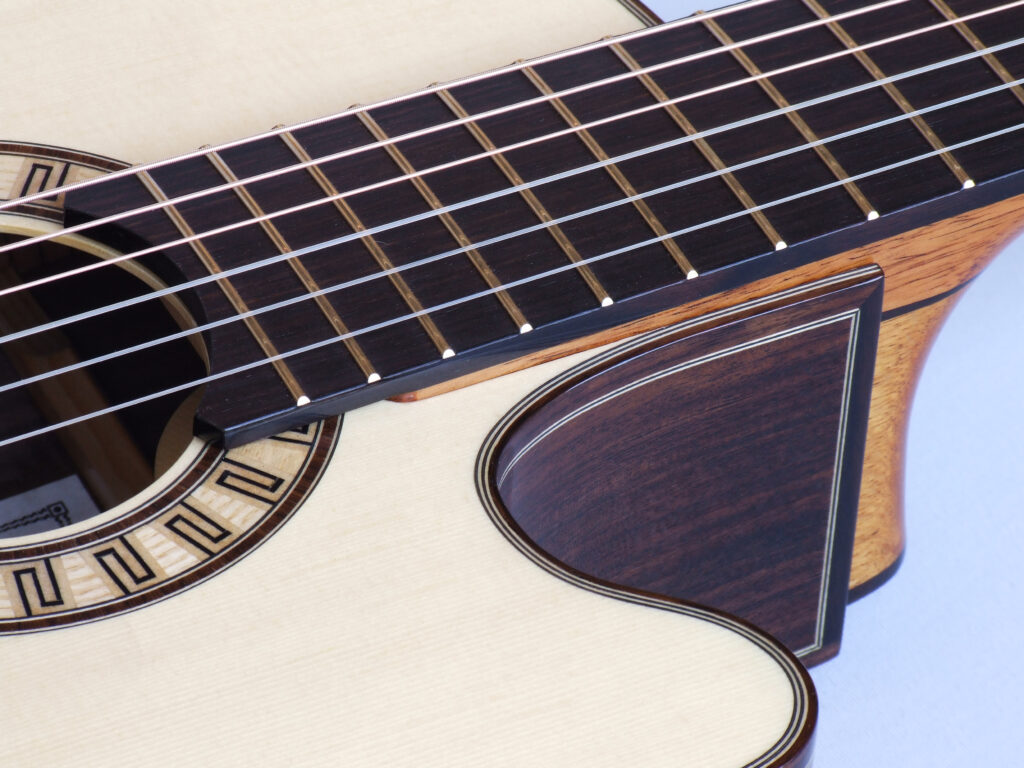
Since 2013 I have been building both classical and steel string guitars with the option of adjustable necks, which means that the neck angle and hence the string action can be adjusted by the player at any time, in a few seconds, without using any tools. You never have to play a guitar with the wrong action ever again!
Straight String Pull
Acoustic guitars with straight(ish) string pulls have been around for a long time. Certainly Johann Stauffer of Austria was using straight string pulls in the early 1800s. It’s hard to say whether this was for acoustical reasons or just so that his guitars could be conveniently hung from a peg using their “Turkish slipper” headstock shape. I use a straight string pull through the nut for both playability and acoustical reasons. The straight string pull means less friction over the nut, easier tuning, better tuning stability and more reliable intonation; all significant benefits to the player. The straight string pull arrangement complements the compensated nuts that I use. As far as I am aware, a three-a-side tuner arrangement on steel string acoustic guitars yielding a straight string pull is unique to me. The innovation here was in staggering the tuners so that they could actually fit into the headstock; it’s impossible to achieve a three-a-side straight string pull with a symmetrical tuner array. It’s also impossible to achieve on a classical guitar using standard slot-head tuners. So to gain the considerable benefits of less friction over the nut, easier tuning, better tuning stability, and more reliable intonation from using a straight string pull, I use planetary pegs on my classical guitars. These look almost identical to traditional ebony tuning pegs but have a gearing arrangement actually inside the body of the peg. They work wonderfully well.
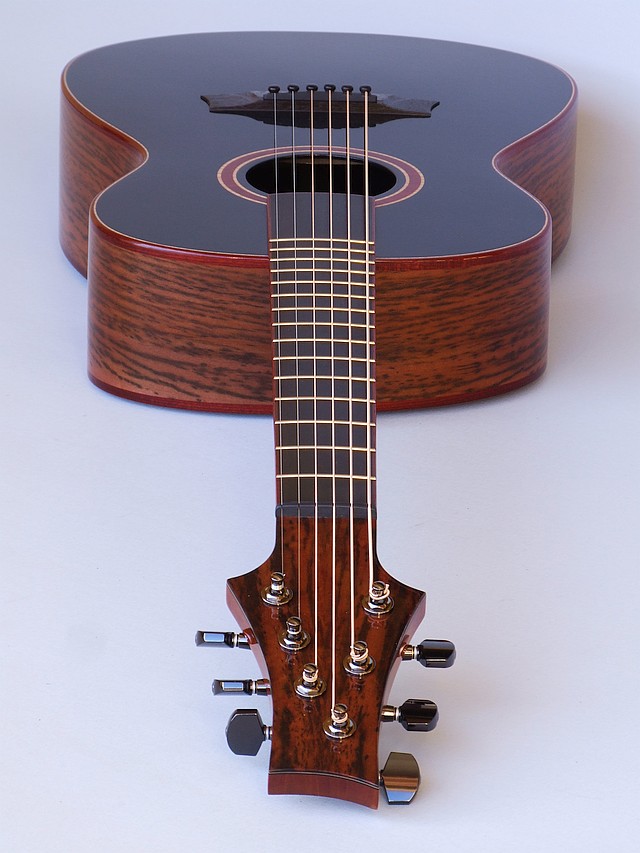
Modal Tuning
The concept of modal tuning is summarised as follows: Guitars radiate sound from their vibrating parts, mainly the top plate. If a guitar top vibrates in a different way, it produces a different sound. The different ways a guitar top vibrates are called modes. If the modes are tuned to resonate at particular frequencies with particular amplitudes, we can shape the way a guitar sounds. Learning how to manipulate the parameters of the modes and, in particular, understanding what the target frequencies should be, has been the focus of my research and development efforts over the last 20 years.
The fruit of this research is manifest in my range of guitars. Modal tuning is intrinsic to gaining consistent acoustical performance from guitars and is how I achieve consistency in my acoustic guitars. Modal tuning is grounded in sound physics and engineering principles, unlike the majority of popular methods that assign “brace tuning” and “tap tuning” to some form of art.
Modal vibrations and modal tuning are the fundamentals behind how guitars work, and why different models of guitar sound different; but the subject has a minuscule following. That’s easy to explain – it involves complex physics and mathematics! For those interested, I run a three day course on the subject, which, so far, I’ve delivered to over 200 luthiers in the USA, Europe and Australia.
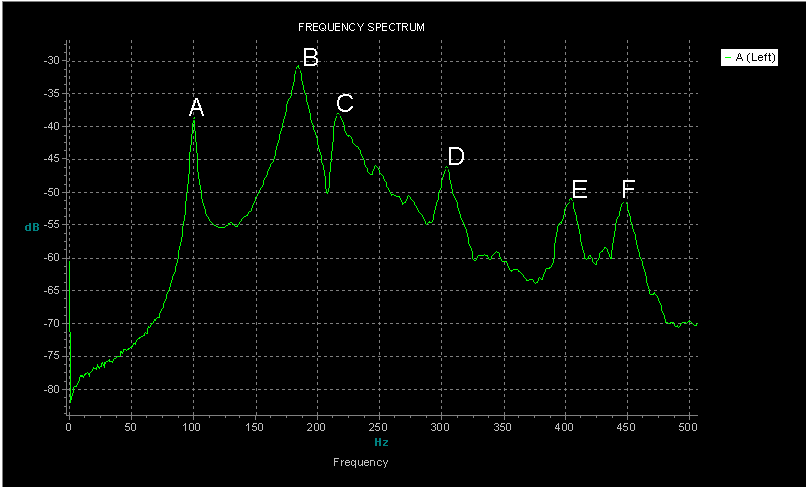
Acoustic Guitar Finishes
Finishes are more important than you might think. Some factories will never produce great guitars whilst they persist with their current finishing schedules. No matter how good the woodwork, the guitars are “killed” by the finish that is applied. A particular culprit in factory guitars is polyester, a high density material with a very high damping coefficient. Many first-time builders use oil based finishes, with similar consequences. Low mass, low damping finishes must be used to reap the possibilities of the best design and construction methods. It also helps if the finish is durable and non-toxic. Nitrocellulose lacquer can produce great results, but it’s hardly non-toxic. Shellac (French polish) can produce great results, but in standard form it’s hardly durable.
My innovation has been to bring together two technologies; hardened shellac, a chemistry which cross links shellac to give it a toughness approaching polyurethane finishes, developed in Australia by Robert Rae and an application chemistry developed in the USA by Brian Burns and the late Dr. Roger O’Neill. The application process that I use I developed myself. This makes a French polish finish reasonably economical to apply (in terms of the time taken, which is normally prohibitive) and non-toxic.
The benefit to the player is one of the most beautiful finishes available, which is also durable and as acoustically transparent as finishes get, without a prohibitive cost. The soundboards of most of the guitars I build, both steel string and classical, are French polished with hard shellac.
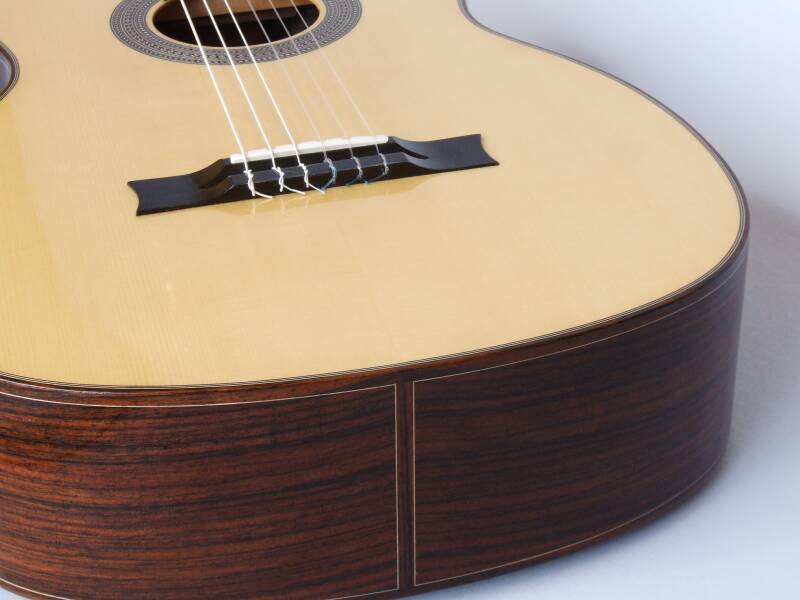
Monopole Mobility
Monopole mobility is a measurement of how much a guitar top will move under the oscillatory forces of the strings. More movement = more sound. It’s not the sole arbiter of a good guitar, but it’s a good indicator; the instrument also has to play in-tune, be even in volume across the strings and frets, and have an alluring tone. But anyone who tells you that the guitars they build are responsive, sensitive, “powerful” etc. should be able to substantiate their claims. I can, using this measure.
My guitars, both classical and steel string, have significantly higher monopole mobility than the average of the comparison guitars, and the comparison guitars included the best guitars I could get my hands on. This doesn’t translate to double the volume (however you choose to measure that!) but it translates to what you hear being very noticeably louder and more responsive than the average.
Research
Since 2015 I’ve been involved with Pacific Rim Tonewoods (PRT) in a project to classify the acoustical properties of spruce tonewoods, ultimately leading to a grading system that ranks tonewood on its acoustical properties rather than just the wood’s cosmetic appearance. The objective was to determine which acoustical characteristics of the timber produced what audible outcomes in the finished guitar and to segregate that wood for the market. Dr David Olson of PRT sets the scene and tells the story of this research in this video. It is engaging and detailed, so allow an hour’s listening time. PRT worked internationally with collaborators in Europe, Australia and the Americas to complete this research and was able to prove unequivocally that specific timber properties (stiffness, density, damping) produced repeatable, audible differences in guitar performance, with low density, low damping wood being distinctly favoured for ultra-responsive guitars, both classical and steel string.
Three steel string guitars, matched in every way (that is every way!) except for the damping coefficient of the top wood can be heard being played by the extraordinarily talented Miroslav Tadić in the video below. One guitar has top wood with a damping coefficient right on the mean value for the species (Lutz spruce) whist the other two guitars have top wood of essentially the same density and stiffness but with damping coefficients plus and minus one standard deviation from the mean (that is around a +/- 10% difference from the mean value of damping). Are you able to tell which is the low, medium and high damping guitar? Check the headstocks: one is marked B, one R and one Y (blue, red, yellow).
Of course, low density, low damping top wood isn’t the right answer for all guitars. High performance wood requires a high performance player to control it. Everything you play is audible, whether you intended it or not, much like a typical city driver would struggle with a Formula 1 car on a race track. So for some styles of music and some styles of playing, wood with properties closer to the mean is more desirable. But with PRT’s acoustically graded wood you can confidently make the right choice for the next instrument you build.
Many thanks to Steve McMinn and Eric Warner of PRT and to Miroslav Tadić for allowing me to post this video.
More videos of Miroslav playing these guitars can be found here.